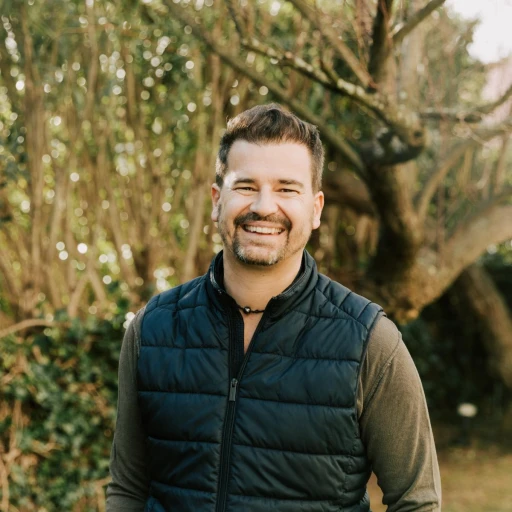
Comprendre les fondamentaux de la maintenance productive totale
Les bases essentielles de la TPM
La Total Productive Maintenance (TPM) est une approche systématique qui vise à améliorer l'efficacité des équipements de production par le biais d'une gestion proactive et préventive. Afin de garantir le succès de cette méthode, il est primordial de bien comprendre ses principes fondamentaux et ses objectifs clés.
La TPM s'articule autour de plusieurs piliers essentiels qui incluent la maintenance autonome, la maintenance planifiée et l'amélioration continue. Ceux-ci permettent d'approfondir la connaissance des équipements et d'accroître la compétence des opérateurs par le biais de formations ciblées.
Amélioration de la performance et de la qualité
En implémentant la TPM, les entreprises cherchent non seulement à réduire les pannes et les interventions de maintenance non planifiées, mais aussi à optimiser la performance qualité de leurs systèmes de production. Grâce à cette gestion proactive, les cycles de production deviennent plus fiables et continus, ce qui se traduit par une amélioration du TRS (Taux de Rendement Synthétique).
Les méthodes de maintenance préventive et prédictive sont intégrées dans le plan de maintenance afin de renforcer la sécurité des opérations et d'accroître la durée de vie des équipements. Pour plus de détails sur l'optimisation des processus, vous pouvez consulter notre article sur la méthode 6 Sigma Lean, un complément efficace à la TPM pour l'amélioration continue.
Identifier les défis spécifiques de l'entreprise
Défis spécifiques liés à l'entreprise
Pour la mise en œuvre efficace de la maintenance productive totale (TPM), il est crucial d'identifier les défis uniques de votre entreprise. Chaque environnement de production est distinct, avec ses propres exigences et contraintes liées aux équipements, opérateurs, politiques de santé et sécurité, et plateformes technologiques. L'importance de détailler ces défis est de permettre une gestion proactive et sur mesure des besoins en maintenance et amélioration continue.
- Évaluation des équipements : Identifiez les machines sujettes aux pannes fréquentes ou celles ayant une influence significative sur le TRS (Taux de Rendement Synthétique). Les interventions de maintenance devraient être planifiées efficacement pour minimiser les arrêts de production.
- Implication des opérateurs : Encourager et former les opérateurs à participer activement à la maintenance autonome peut réduire les petits dysfonctionnements qui ne nécessitent pas l'intervention d'une équipe de maintenance.
- Environnement de travail : Les lieux de travail doivent répondre à des normes de sécurité élevées pour soutenir les pratiques de TPM et éviter des accidents ou incidents qui pourraient retarder la production.
En abordant ces défis, vous créez une base solide pour une mise en œuvre réussie de la TPM. Pour une approche approfondie, vous pouvez envisager la marche Gemba afin d'obtenir une connaissance directe des processus de production dans un cadre réel.
Mise en œuvre de la TPM : étapes clés
Étapes essentielles pour implanter la TPM
La mise en œuvre efficace de la maintenance productive totale (TPM) repose sur plusieurs étapes clés qui garantissent une transition en douceur vers un système de gestion rigoureux et performant. Voici quelques étapes cruciales qui facilitent cette transition :- Sensibilisation et formation des équipes : La formation des opérateurs et du personnel technique est indispensable. Cela inclut la formation à la maintenance autonome et la capacité à identifier et résoudre des problèmes mineurs, limitant les pannes inopinées.
- Évaluation initiale des équipements : Établir une base de référence de l'état actuel des équipements de production permet de planifier les interventions de maintenance préventive et corrective. Le Total Productive Maintenance se poursuit en analysant le TRS (Taux de Rendement Synthétique) pour mesurer la performance actuelle des équipements.
- Développement d'un plan d'intervention : Planifier des actions de maintenance planifiée et de maintenance préventive avec des objectifs clairs et mesurables contribue à accroître la performance et la sécurité des systèmes de production.
- Mise en place d'indicateurs de performance clés (KPI) : Ces indicateurs permettent de suivre la progression des efforts de TPM. Des exemples incluent la réduction des pannes, l'amélioration de la qualité de production, et l'optimisation des coûts de maintenance.
Mesurer le succès de la TPM
Évaluation continue et ajustement du TPM
Dans le cadre de l'amélioration continue des processus de production, il est essentiel de mesurer régulièrement le succès de la maintenance productive totale (TPM). Voici quelques approches spécifiques pour y parvenir :- Suivi des indicateurs clés de performance (KPI) : Les indicateurs tels que le temps moyen entre deux pannes (MTBF), le temps moyen de réparation (MTTR), et le taux de rendement synthétique (TRS) sont des mesures essentielles pour évaluer l'efficacité des interventions de maintenance et l'amélioration de la performance des équipements.
- Analyse de la qualité de production : L'amélioration de la qualité est un signe indiquant que les processus de TPM fonctionnent bien. Une réduction des défauts de production et des retours clients démontre une gestion efficace de la maintenance préventive et prédictive.
- Évaluation de la productivité des opérateurs : En observant la façon dont les opérateurs interagissent avec les équipements après les formations de maintenance autonome, il est possible de mesurer le niveau de compétence atteint et l'impact sur la productivité totale.
Utilisation des retours d'expérience pour des ajustements
L'un des aspects cruciaux du TPM est la capacité à intégrer les feedbacks des équipes au quotidien. Cela permet non seulement de faire des ajustements rapides, mais aussi d'impliquer davantage le personnel opérateur et de renforcer la culture de sécurité au sein de l'entreprise.- Chantiers Kaizen : Ces ateliers permettent de rassembler régulièrement les équipes de travail pour discuter des problématiques rencontrées, analyser les données de performance, et proposer des solutions créatives qui améliorent les résultats de la maintenance TPM.
- Comité de pilotage : L'existence d'un comité assure un suivi rigoureux des projets de mise en œuvre et permet de comparer les résultats avec les objectifs fixés. Cela garantit que la méthode TPM reste sur la bonne voie et continue de produire des bénéfices significatifs.
Surmonter les obstacles à la mise en œuvre
Dépasser les Obstacles liés à la Mise en Œuvre
La mise en œuvre de la maintenance productive totale (TPM) ne se fait pas sans difficultés. Plusieurs obstacles peuvent freiner sa réussite, mais en les identifiant clairement, on peut les surmonter plus efficacement.
- Résistance au changement : L'adoption d'une nouvelle méthode de gestion, comme la TPM, nécessite un engagement de l'ensemble de l'organisation. Les opérateurs et le personnel de production peuvent parfois être résistants en raison d'un manque de formation ou de compréhension. La formation continue et l'implication des équipes dans le processus de mise en œuvre sont essentielles.
- Manque de ressources : Souvent, les interventions de maintenance tpm nécessitent des ressources considérables, tant humaines que matérielles. Il est crucial de prévoir un budget suffisant et de gérer les ressources existantes de manière stratégique pour maintenir la qualité et la performance des équipements.
- Gestion des interventions de maintenance : La coordination pour garantir qu'aucune opération productive ne soit arrêtée se révèle parfois être un véritable défi. Les méthodes de maintenance préventive et predictive doivent être intégrées de manière à minimiser les pannes imprévues et à améliorer la sécurité.
- Suivi de la performance : Mesurer le succès de la TPM à travers des indicateurs pertinents comme le taux de rendement synthétique (TRS) est indispensable pour ajuster les stratégies. Une gestion efficace du projet tpm nécessite de constamment analyser les résultats et ajuster les tactiques selon les besoins.
Surmonter ces obstacles exige une attention concentrée sur la gestion de maintenance efficace et un engagement total envers la méthode TPM. L'amélioration de la qualité et de la performance totale des processus de production est atteignable grâce à un travail collaboratif et une mise en place rigoureuse des piliers TPM.
Études de cas : succès de la TPM dans d'autres entreprises
Succès remarquable grâce à la TPM
Dans le cadre de la mise en oeuvre de la TPM, plusieurs entreprises à travers différents secteurs ont réussi à transformer leur gestion des opérations et à améliorer leur performance globale. Voici quelques exemples inspirants :
- Amélioration continue chez un fabricant de pièces automobiles : Grâce à l'application des piliers TPM, cette entreprise a réduit ses pannes d'équipements de 30 % en moins d'un an. L'implication des opérateurs dans la maintenance autonome a joué un rôle clé dans cette réussite, permettant un contrôle accru de la qualité et de la sécurité des processus de production.
- Optimisation de la production dans une entreprise agroalimentaire : Un projet TPM a permis d'identifier les interventions maintenance les plus critiques, augmentant ainsi le TRS (Taux de Rendement Synthétique) de 20 %. La formation des équipes a encouragé une meilleure gestion de la maintenance, favorisant une efficacité totale.
- Réduction des coûts dans une usine de composants électroniques : Par l'implémentation d'une maintenance préventive bien planifiée, cette société a pu non seulement augmenter sa qualité productive, mais aussi réduire considérablement ses coûts opérationnels. La TPM totale y a été perçue comme une méthode incontournable pour maintenir la compétitivité sur le marché.
Ces exemples démontrent combien une gestion intelligente et proactive des systèmes de maintenance est cruciale pour la performance qualité et l'efficacité productive de l'entreprise.